2017年作成
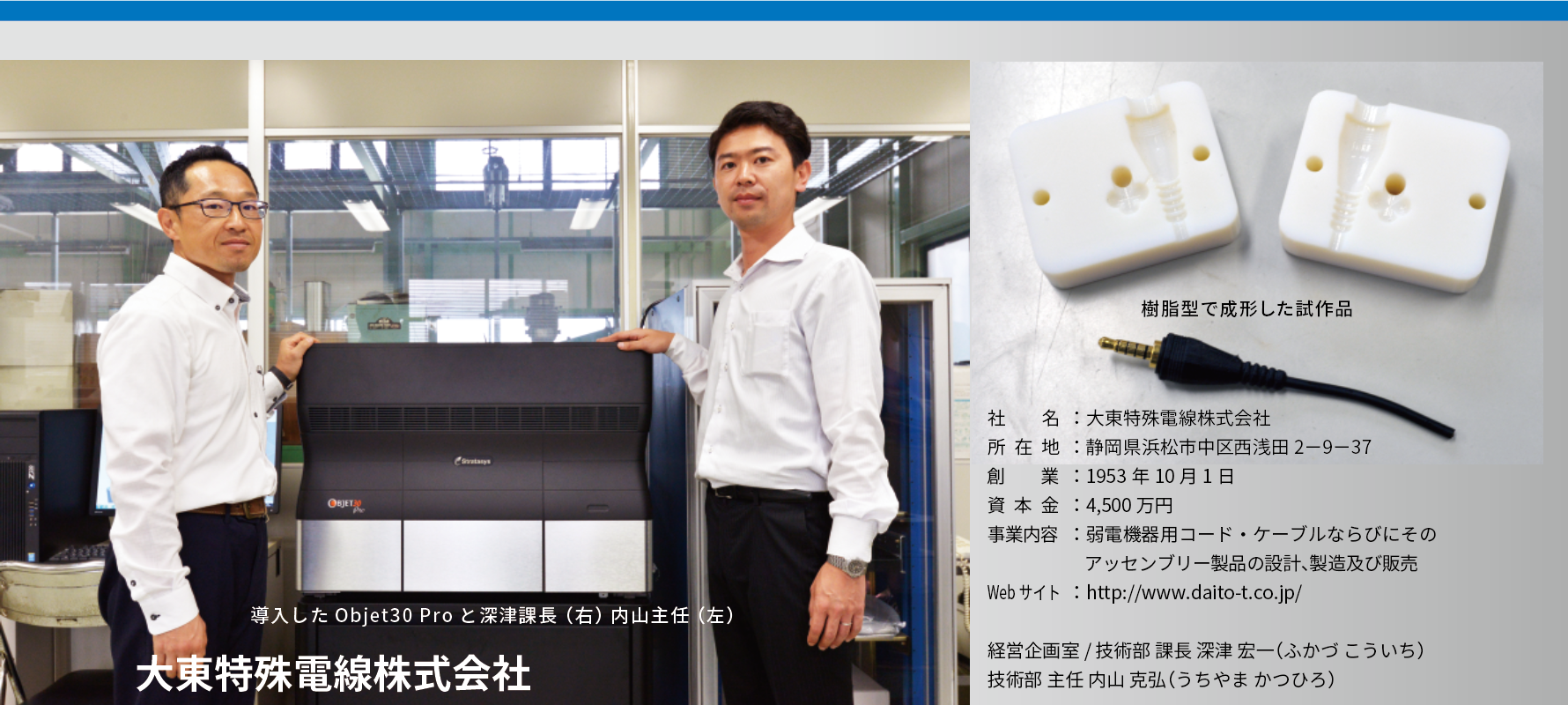
3Dプリンターで樹脂型を造形して金型作製前に耐久テストをしています。
大東特殊電線株式会社は、1953年に設立された弱電機器用コードやケーブルの設計・製造を行っているメーカーである。
製造工場を海外に置く同社は、新製品の設計・試作は国内で行っている。
ケーブルの開発にあたっては、金型を作製してから成形し、デザインや強度の確認を行っていたが、2013年に3Dプリンターを導入。
金型の作製前に3Dプリンターによる樹脂型での成形を行うことで開発期間を大幅に短縮した。
さらに、以前は顧客からの注文を受けて開発をしていたが、3Dプリンターで作製した試作品を活用することで、提案型の営業を行うことも可能になったという。3Dプリンターの導入・活用を推進している同社の経営企画室 / 技術部 深津課長、技術部 内山主任にお話を伺った。
※2017年取材時点の内容
お客様情報
社 名 :大東特殊電線株式会社
所 在 地 :静岡県浜松市中区西浅田2-9-37
創 業 :1953年10月1日
資 本 金 :4,500万円
事 業 内 容 :弱電機器用コード・ケーブルならびにそのアッセンブリー製品の設計、製造及び販売
Webサイト :http://www.daito-t.co.jp/
特殊なコードやケーブルをオーダーメードで開発・製造
貴社の事業について教えてください。
深津課長:弊社は電線を製造している会社です。
電気を大量に流さない、弱い電気を流すタイプの細い電線、長いケーブルの場合はそれを切って端末にコネクタをつけるといったことを行っています。
もともとは電話機の受話器についている電線の加工から始まったんですが、細くてしなやかで柔らかい電線(ケーブル)に特化していきました。細くて柔らかい電線、曲げに強い電線、細くて規格もないような電線をオーダーメイドで作っています。
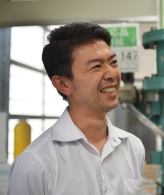
3Dプリンターに興味を持ったきっかけは?
深津課長:最初は3Dプリンターって面白そうだなと思ったのがきっかけでした。端末の加工をするときに、屈曲を気にしながらデザイン設計するんですが、今までは金型を作り、サンプルを成形し、耐久テストをしてから、その結果を検証していました。
金型を作ると一発勝負なところがあるので、慎重になってしまいます。しかし、3Dプリンターであれば柔らかいサンプルを造形できるんじゃないかと思いました。
2012年ごろ、オバマ前大統領がこれからは3Dプリンターの時代と言っており、私たちもそう考えていました。
3Dプリンターはどのような基準で選びましたか?
深津課長:最初は軟質の造形ができるといいなと考えていました。
私たちが作るケーブルは軟質のPVCや軟質のエラストマーなので、そういったもので造形できる機械を内山と二人で探していました。
3Dプリンターを購入してからどのくらいで軌道に乗りましたか?
深津課長:軌道に乗るまで2~3か月でした。
3D-CADは以前から使っていたんですか。
深津課長:3Dプリンターを導入するかもしれないと考えて対応できる3D-CADソフトのリースを増やし、3D-CADの習得も内山にさせていました。
樹脂型で金型修正のリスクを減らす
導入後に何か変化はありましたか。
深津課長:一番多かったのは金型の部分で、樹脂型を作っていると「これできる?」って気軽に検証依頼が来るようになったことですね。
3Dプリンターで樹脂型を造形して、その型で作ったものとその試験結果をお見せしたりということです。
それまでは金型を作ってから試験をしていたのでリスクが高かったんです。試験で失敗したら金型が使い物にならなくなりますが、今は樹脂型で確認することができます。
当初から樹脂型を検討していたんですか?
深津課長:最初は、ゴムライクのサンプル造形を御社(アルテック)に依頼して、できあがったサンプルを社内の会議で見せました。
社内でもそんなことができるのかと好評だったんですが、私たちは耐久試験までできるものではないと判断をしました。
内山主任:最終製品と同じ樹脂を使わないと生産の際にどういった不具合が起きるかわからないので。
深津課長:だったら樹脂で型を作って、そこから何回か射出成形ができるんじゃないかとなり、樹脂型のデータを作って、御社に造形をお願いしたところ、問題なくできました。
樹脂型だと耐久性は少し下がりますが必要な数は取れるということで3Dプリンターの購入を決定しました。
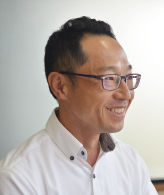
樹脂型は何種類くらい作っていますか?
深津課長:金型のベースが今は2つあって、そこに入れ込む入子型を作るんですが、それは20~30個ほど作っています。
金型はどのくらいの期間でできますか。
深津課長:金型は中国で作っています。昔は日本で作っていたんですが、それでも1ヶ月くらいかかりました。今は中国のメーカーに依頼しており、1ヶ月半から2ヶ月ほどかかります。
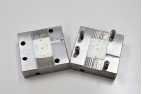
組み合わせて
射出成形
樹脂型はどのくらいの期間でできますか?
内山主任:樹脂型なら2日くらいですね。3Dプリンターにデータを送ってから半日ほどで造形できるので、次の日の朝に来るとできているって感じです。
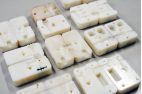
樹脂型
1つの型でどのくらい作れるのですか?
内山主任:形にもよりますが、単純なものであれば50個くらい。うまくいかないときは3個ほどです。薄肉の部分が圧力で折れてしまうんです。
深津課長:ただ、曲げの試験は5個とか10個単位なので、少なくとも3個取れるのであれば、樹脂型をいくつか作ることで対応できます。
以前は、金型を起こして失敗したら大惨事でした。それでもやらなきゃいけない。中国から金型が戻ってきて、射出成形して、その試験結果がだめだったらもう1回金型を改造・修正していました。それが今だったら1週間で2、3個の樹脂型を作り、検証できる。
内山主任:検討段階ではいいなと思っても、樹脂型を作ったらだめだったということもあります。
深津課長:樹脂型よりも金属型の方が精度は高いので、樹脂型で成功するなら金属型では絶対に成功します。
樹脂型で問題なければ、金型を起こしても失敗がない?
深津課長:まずないと言っていいと思います。ないよね?
内山主任:ないない。金属のほうが精度も条件も振れるじゃないですか。
樹脂成型のときは圧力や樹脂の温度といったパラメーターをいじりながらやらなきゃいけないけど、金属型は最適な条件で出せて、仕上がりも綺麗にいったりする。
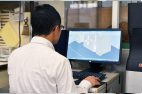
3D-CADの データを
修正して再度検証
深津課長:金型を修正しなくてよくなったというのが一番のメリットですね。
内山主任:樹脂型すごいよね、そういう意味で。僕らにしてみると夢のようですよ。同じ材料でテストできて、だめならいつでもやり直せる。金型もいじらなくていい。
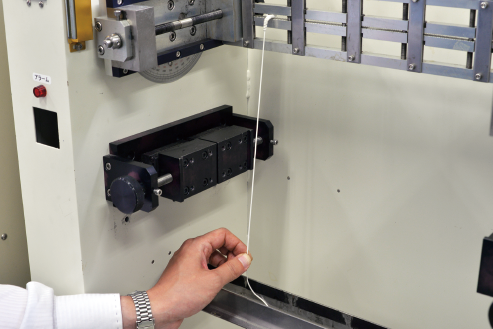
1万回以上曲げても破損しないかをチェック
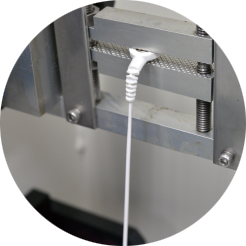
3Dプリンター導入前と導入後の工程比較
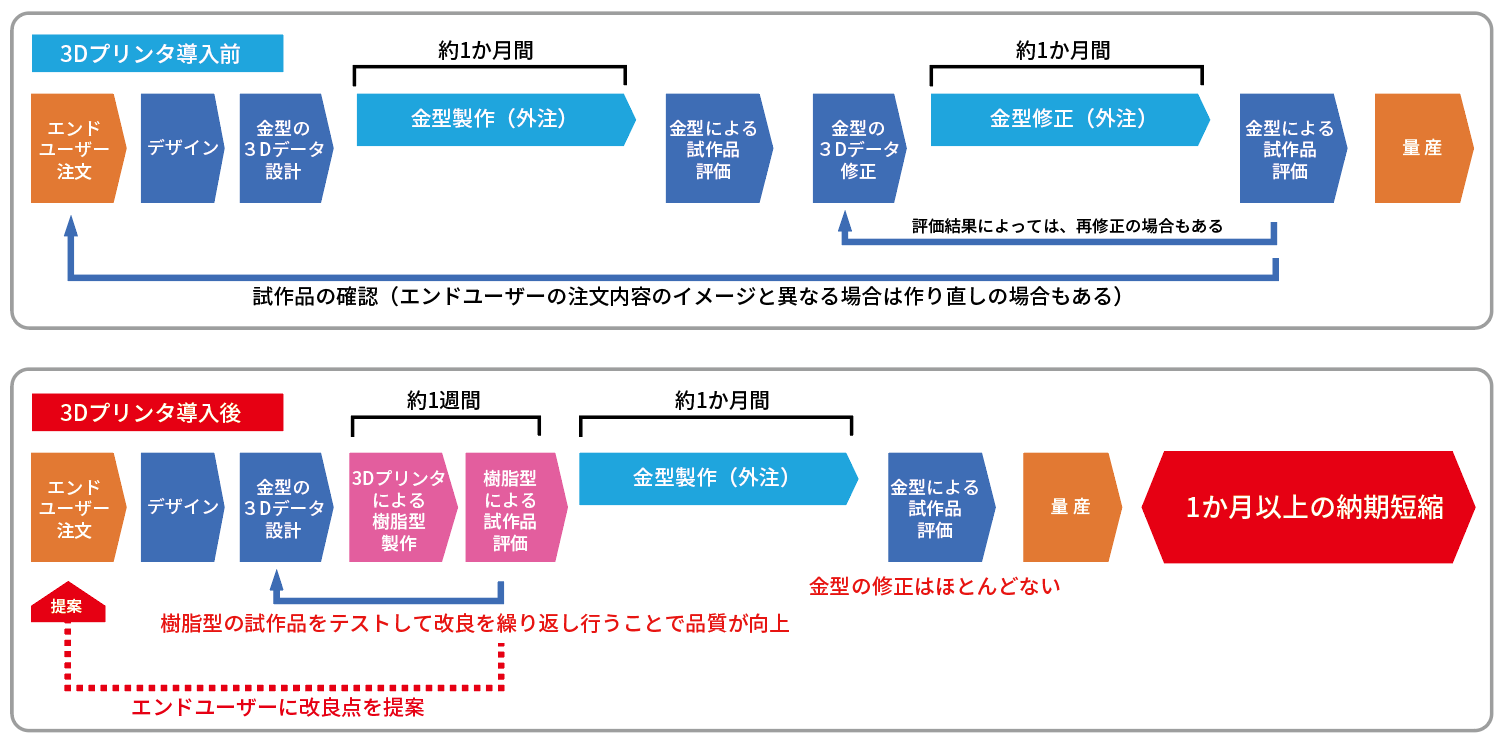
樹脂型を製品開発の提案ツールに
深津課長:あるヘッドフォンの企画で3種類ほど金型を作ることになったんです。
その製品はデザイナーの指定するケーブル・デザインが複雑でデザインの再現とヘッドフォンの強度、引っ張ったり曲げたりしても切れないといった品質保証が同時に求められるものでした。
それは大変そうですね。
深津課長:これまでの経験で「一発勝負で金型を起こしてできないか」と相談されたのですが「5~10本くらいなら樹脂型を起こせばできますよ」と提案したんです。
ただ、そんなこともできるんなら、あれもこれもって求められて、むしろ金型を起こしたほうが立ち上げ自体は早かったかなって(笑)。
でも、お客様にあまり費用負担をかけずに、いろいろと試してもらえたのでよかったと思います。
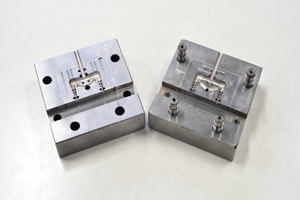
そこが一番変わったところですね。
深津課長:もう順序が変わりましたね。前は、「お願いします。変えさせてください。良くなると思いますので」というところだったのが「こうなります。データもあるので結果的に良くなるからやらせてください」って変わりました。
「試験してこれだけ違うから、やったほうがいいですよ」と言えるんです。
樹脂型以外では何を作っていますか?
深津課長:固定治具やプラスチックで切削したら面倒なパーツはちょこちょこ作ってますね。フライスや旋盤で削れば色々できるんでしょうけど大変なので。
どういった治具を作るんですか?
深津課長:例えば、製品の上にずれないようにシールを貼らなければいけない場合に、位置がずれないようにするためのものとかですね。そういったものは挙げていけばキリがないですね。
内山主任:3Dプリンターを入れている企業はどこもやっているとは思いますが。
今後、3Dプリンターを活用してこんなことをやりたいといった構想はお持ちですか?
深津課長:樹脂型で作ったものを市場に出せるだけのクオリティに仕上げて、オリジナル製品を作れたら面白いなと思います。
内山主任:現状はポリゴンぽさが出るというか、円柱を作ったときなどはカクカク感が出てしまうので。
深津課長:将来は販売できるものを直接作れると面白いんですけどね。
ありがとうございました。
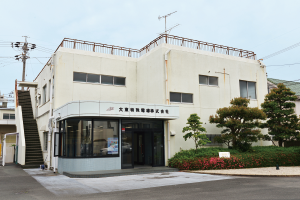
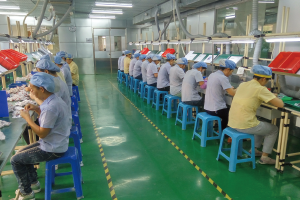
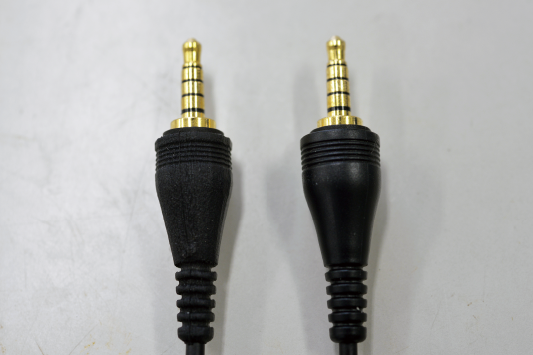
ご協力ありがとうございました。
※上記コメントはお客様の個人のご意見・ご感想であり、当社の見解を示すものではありません。
この事例で登場した製品
Objet30Pro(生産終了品・後継機種あり)
小型ながら上位機種にも引けを取らない人気機種。アクリルベースの材料を使用して微細な形状もしっかり表現。樹脂型としての活用も可能!