インクリメンタル成形とは
2025年03月10日
専用の工具を使用して金属板に圧力を加え、凹凸を形成することで三次元形状を成形する技術です。インクリメンタルフォーミングとも呼ばれます。
数十年前から存在する技術で、板金加工を必要とする様々な分野で活用が期待されています。そのため、さらなる応用可能性を追求する研究開発が進められています。
ここではインクリメンタル成形についての基本情報と、最新のインクリメンタル成形技術を用いた装置についてご紹介いたします。
インクリメンタル成形について
インクリメンタル成形は、ペンのような形状の工具を金属板に押し付け、少しずつ変形させながら最終形状を完成させます。
凹凸を層のように重ねて、少しずつ深くしていくことで成形します。そのため平らな面だけでなく、ドーム型のように湾曲した面を作り出すことも可能です。
このように、ピンポイントに力を加えながら、徐々に完成品に近づけていく加工技術を総称して、逐次成形といいます。
従来の板金加工では、技術者の手作業や、金型を製作してプレス加工を行う方法が一般的でした。
インクリメンタル成形は金型を必要とせず、必要な形状をダイレクトに形作ることができます。
インクリメンタル成形の対象となるものの例
主に下記のような用途で活用が期待できます。
- 自動車業界:車のボディ・部品などの試作や、コンセプトカーなど展示用車の実部品。
- 航空宇宙業界:航空機の機体や部品の試作。
- 建築業界:建造物の内装や外装に使用するパーツ。
その他にもあらゆる板金加工が行われるシーンで、インクリメンタル成形は有効です。
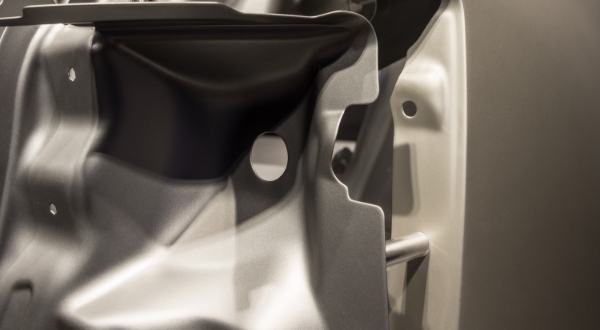
インクリメンタル成形の方式
成形物の品質を高めるために研究開発が進められており、その成形方式は大きく2つに分けることができます。
シングルボール式
使用する工具が1つで、金属板に片面からのみ力を加えて成形する方式です。
先端が球状の工具を使用することが多いため、「シングルボール」と呼ばれます。
シングルボール式はさらに2つの方式に分けることができます。
下型なし方式
金属板の下に、専用の台座などは設置せず成形を行う方式です。
くぼみのある台座を汎用的に使用することもあれば、金属板を浮かせて固定することもあります。
成形したい形状に応じた下準備などが不要なため、手軽に成形を行うことができます。
その一方で、成形物の品質は低い傾向にあります。
下型あり方式
金属板の下に、簡易的な下型を設置して成形を行う方式です。
下型は技術者が手作業で製作する、もしくは下型なしのインクリメンタル成形で製作する方法があります。
下型があることで予測不能な変形を防ぐことができ、下型なし方式に比べて成形物の品質を高めることができます。
しかし、簡易とはいえ下型を製作する必要があるため、手間やコストがかかります。
デュアルボール式
金属板の表側から力を加えて成形を担う工具と、裏側から素材をサポートする工具の2つを使用する方式です。
金属板の変形を精密に制御できるため、シングルボール式に比べて成形物の品質が高く、より複雑な形状の成形も可能です。
ですが、工具を動かす装置の制御が複雑なため、実用化にはまだ課題があります。
また、装置の導入コストの高さも懸念されます。
インクリメンタル成形のメリット
インクリメンタル成形を活用することで、どのようなメリットがあるのでしょうか?
板金加工を行う製造業などにおける課題と照らし合わせて解説します。
納期短縮
技術者による手作業やプレス加工では、試作品を一つ作るにも多くの時間を要していました。
理由として、手作業で板金加工を行うには高い技術が必要なため、その工程を担える人材が少ないことが挙げられます。またプレス加工に必要な金型は外注することもあり、製作に時間がかかります。
そこでインクリメンタル成形機があれば、金型を必要とせず、設計した形状にダイレクトに成形することが可能になります。
下型を製作するとしても、プレス加工機の金型に比べると簡易的な型で済むため、最終品の完成までにかかる時間は短縮できます。
コスト削減
金型の製作には、時間だけでなくコストもかかります。
特に試作工程では、完成したものを元に複数回の調整ややり直しが発生します。その都度金型を作るには、コストがネックになっている現場も多いのではないでしょうか。
インクリメンタル成形機で試作品を製作することで、コストを抑えてより手軽に試行することができます。
それはコストメリットだけでなく、最終的には実製品の品質向上にも繋がります。
省スペース化
量産に使用した金型を、補給部品が必要となった際のために何年も保管しておかなければならないというケースがあります。
新製品が製造される度に金型が増えていく一方で、保管場所の確保が負担になっています。
インクリメンタル成形は、一つあたりの成形時間ではプレス加工よりも時間がかかるため、量産フェーズでは現状普及していません。
しかし、オーダーメイド品や補給部品のような多品種少量生産においてはアドバンテージがあります。
金型をそのまま保管するのではなく、インクリメンタル成形のための造形データとして保管することで、省スペース化を実現します。
インクリメンタル成形の課題
インクリメンタル成形の活用で様々なメリットがありますが、同時に課題もいくつか挙げられます。
成形に時間がかかる
試作フェーズでは納期を短縮するメリットがあるインクリメンタル成形ですが、量産フェーズでは課題があります。
金属板を金型で挟み込むプレス加工に比べると、金属板に凹凸を作り出すことで少しずつ成形するインクリメンタル成形は、どうしても時間がかかります。
そのため現状は試作品の製作や多品種少量生産などの用途に限定されています。
成形品質が低い
インクリメンタル成形による成形物は、表面に凹凸が表れやすいです。
また下型なしで成形した場合、想定とは異なる変形が発生することもあります。
試作としての活用であれば十分ですが、最終製品としてそのまま使用するのは難しい現状です。
そのため最終製品として活用する際は、研磨を行うまたは見た目が重視されない箇所に使用するなどの工夫が必要です。
従来方式の課題を解決する、新しいインクリメンタル成形
インクリメンタル成形の課題を解消し、より広い用途で活用するための技術開発が進んでいます。
中でも、金属板に押し当てる工具と下型に代わるマットを独自開発し、注目を集めている成形機があります。
Figur社が開発した板金加工成形機は、インクリメンタル成形のメリットをそのままに、成形品質を向上させています。
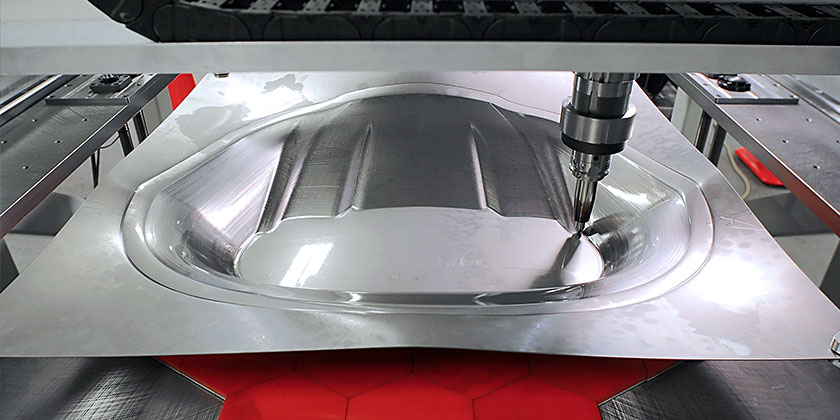
金属板に圧力を加えて成形する「ツールヘッド」はデジタル制御されており、従来のインクリメンタル成形機に比べ、表面を滑らかに仕上げます。
また、下型ではなく汎用的に使用可能な「バックプレート」を下に敷くことで、成形時に金属板にかかる圧力の分散を防ぎ、ピンポイントに凹凸形状を作り出すことを可能にしています。
これらの「ツールヘッド」と「バックプレート」はFigur社が特許出願中の独自技術です。
成形品質が高く、下型が不要なためさらなる納期短縮を実現します。従来のインクリメンタル成形機に代わる存在として期待が高まっています。
この記事の監修者
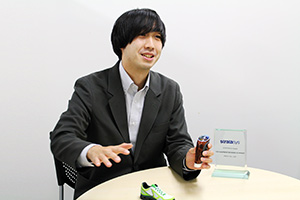
日々お客様からいただく生の声を糧に、「今、本当に求められている情報」をWebサイトやWebセミナーで精力的に発信している。