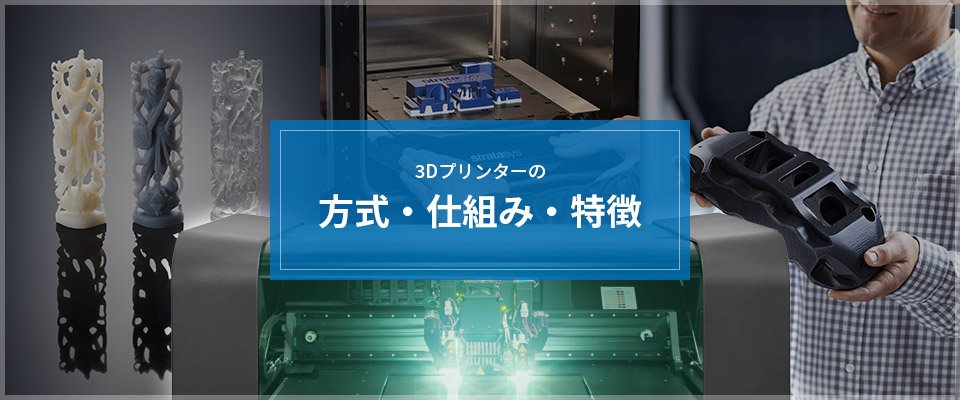
最終更新日:2025年1月27日
3Dプリンターとは3D CADデータを元に3次元の立体造形物を出力(プリント)する装置です。
3Dプリンターには様々な方式があります。
基本的にはどれも1層1層積んでいく仕組みですが、方式によって得意不得意があります。
方式によって、造形物の精度、扱える材料とその物性、造形可能なサイズ、スピード、メンテナンス性など、様々な特徴の差異があります。
また、メーカー各社の独自用語が存在するなど、同じ方式を指していてもそれを表す用語がいくつもあるケースがあり、全体像の把握には、それら表記ゆれに対するケアが必要です。
3Dプリンターの方式はISOで分類が規定されておりますので、その区分を参考にしながら、主要な方式を網羅的にまとめました。
3Dプリンターの仕組み
3Dプリンターは材料を1層1層積み上げていくことで、高さのある造形物を出力します。
様々な方式はありますが、基本的に層を重ねていくことで造形するという点に変わりはありません。
そのように、原理としては非常にシンプルです。
扱える材料も、プラスチック(樹脂)、金属、カーボン等、様々な材料を使って造形することができます。
3Dプリンターとは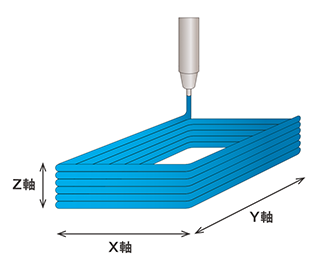
FDM方式
- 日本語表記:熱溶解積層方式(Fused Deposition Modeling)
- ISO分類:材料押出法(Material Extrusion)
- その他表記:FFF方式(Fused Filament Fabrication)
FDM方式の概要
FDM方式とは、3Dプリンター世界シェアNo.1である米国Stratasys社が開発した方式です。
現在3Dプリンターにおいて主流の方式です。
FDM方式による造形
熱で溶かした樹脂をノズルから押し出し、ソフトクリーム製造機のようなイメージで、一筆書きで1層1層積み重ねて造形していきます。
この画期的な方式はストラタシス創設者のスコットクランプがグルーガンを見て想起したという逸話が残っています。
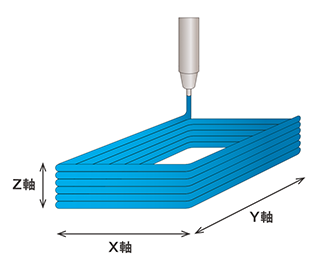
FDM方式の強み
本物の熱可塑性樹脂を使えること、だからこその強度・耐熱が強み
熱可塑性樹脂は射出成形で用いられており、量産する最終製品でよく使われるプラスチック材料です。代表的なものにABS樹脂等があります。
そのため、試作(プロトタイプ)であっても、最終製品に近い物性のリアルで機能的な試験も可能であり、製造業において重宝されています。
他の方式では紫外線硬化樹脂を用いるものが多いため、ABSそのものではなくABSに近い物性を持つ「ABSライク樹脂」が開発されています。
多様な物性の素材が使える
FDM方式、特にハイエンド機種では産業界で求められる様々な物性の樹脂に広く対応しています。
エンジニアリングプラスチック、スーパーエンプラまで使えるなら、特殊用途の最終製品まで使えるイメージが沸くのではないでしょうか。
段差も目立ちにくいキメの細かな機種も
初期の頃は層を積み上げた際にできる段差が目立つ傾向がありました。
しかし近年では、材料も装置も進化していることから、従前より段差も目立ちにくくなりました。
FDM方式の弱点
FDM方式は比較的積層痕が目立ちやすいため、物性よりも外観のなめらかさ、プロダクトデザインにおける表現力を重視する用途では、FDM方式よりインクジェット方式の方が適していると言えるでしょう。
また、FDM方式だけでは金属の造形ができません。そのため、金属で造形したい場合は金属専用の3Dプリンターを導入する必要があります。(※FDM方式と組み合わせて金属造形するシステムは存在します。)
どのようなシーンで選ぶべきか?
製造業における試作(ラピッドプロトタイピング)、治具・工具の製作、最終製品の造形をしたい場合で、強度が求められるものはFDM方式を選ぶと良いでしょう。
光造形方式
- ISO分類:液槽光重合法(Vat PhotoPolymerization)
- その他表記:SLA方式(Stereo Lithography Apparatus)
光造形方式はSLA方式とも呼ばれます。
さらにSLAの中には、レーザー光を用いるレーザー方式と、一括面露光をするDLP方式があります。
光造形方式の概要
光造形方式は、最も古い3Dプリンターの方式です。
液体状の光硬化樹脂のプールに光を照射し、1層1層重ねて造形します。
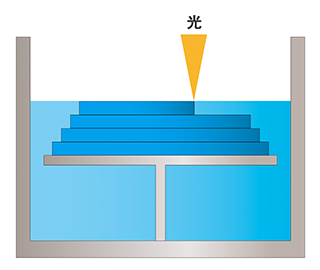
レーザー方式
レーザー光を照射し、光に触れた箇所が硬化される仕組みです。光造形方式の中でも古くからある方式です。
DLP方式
プロジェクターのように像を作り、一括面露光する仕組みです。
造形物の面積が広い場合はレーザー方式と比較して高速露光できることが強みですが、像を作る際、ピクセル単位で描画することから、照射する範囲を広げると解像度が落ち寸法精度が出にくく、また造形物の表面は水平・垂直の両方向に積層痕(段差)が出てしまいます。
光造形方式の強み
きめの細かな造形物が作りやすいこと、個人向けでは安価なモデルが多数登場していることが挙げられます。
造形速度は比較的速い傾向があります。
光造形方式の一般的な弱点
産業用途の光造形機は高額なものが多く、コストが高くなりがちです。
紫外線硬化樹脂を用いるという性質から、太陽光など光による劣化が起こりやすくなる性質があります。
吊り下げ方式のため大型のモデルの造形に適していなかったり、変形が起こる可能性もあります。
そのため、耐久性を求める用途、最終製品として用いる用途ではベストとは言えません。
また、造形後のアルコールや溶剤での洗浄や二次加工、剥離によるサポート除去など後処理に手間が掛かるものが多いです。
どのようなシーンで選ぶべきか?
歴史的経緯として古くはラピッドプロトタイピングに多く使われてきましたが、3DプリンターのDDM(デジタル・ダイレクト・マニュファクチャリング:最終製品や治工具の製造に3Dプリンターを利用する)が浸透するにつれ、役割は変わりつつあると感じます。
個人向けの3Dプリンターでは良い機種が揃ってきていますので、強度・耐久性を必要としないシーンで小さなサイズのモデルを手軽に造形したい場合にお勧めです。
光造形方式による実生産を可能にする進化機種が登場
光造形方式の3Dプリンターの弱点を克服した旧バージョンOrigin Oneから、
実生産活用に向けてさらに進化したOrigin Twoが新登場。
造形品質を向上し、造形材料もさらに拡充。
一方で価格は、旧バージョンのOrigin Oneからかなりお求めやすくなりました。
インクジェット方式
- ISO分類:材料噴射法(Material Jetting/マテリアルジェッティング)
- その他表記:PolyJet方式※Stratasys社
インクジェット方式の概要
インクジェット方式という通称もありますが、正式分類では材料噴射法と言います。
その名の通り、材料を噴射し、それに対し光を当てて1層1層積んでいきます。
構造が2Dプリンターでいうインクジェットプリンターに類似していることから、インクジェット方式と呼ばれています。
高精細でリアルな造形物を作ることができる方式です。
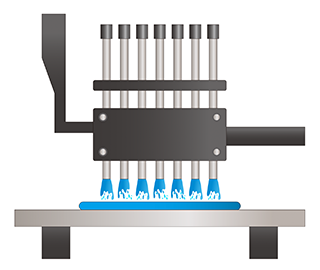
インクジェット方式の強み
高精細な造形物
第一に、高精細な造形物を作ることができるということが挙げられます。
積層痕の目立たないなめらかな造形物を作りたいなら、まず選択肢にあげると良いでしょう。
機種によってはカラー材料の使用や、フルカラー造形も
紙にカラー印刷できるように、3Dプリンターでもカラー印刷できる機種があります。
その原理は、2Dプリンターが複数カラーのインクを用いてカラー印刷を可能にしているのと同様で、複数のカラー材料を用いることで色を再現します。
後から塗装をする必要がなく、塗装時間の短縮や手間を省く事ができます。
上位機種ではPANTONE®カラー対応のフルカラー造形が可能な機種もあり、色にこだわるプロダクトデザインで、完成物とのイメージ乖離を防ぎます。
透明なクリア材料や、ゴムの質感の再現まで
複数の材料を同時に扱うことができる機種もあります。
アッセンブリ加工が必要なものが、ワンショットで造形できます。
デザイナーが思い浮かべたプロダクトのコンセプトを何もない所から具現化する強力なツールとなるでしょう。
3Dプリンターが描く未来の世界に最も近いものがこのインクジェット方式の3Dプリンターかもしれません。尚、この分野はストラタシス社がかなりリードしています。
布や皮革の生地に対して直接3Dプリントできる機種も
麻やフェルト、スウェードや皮革などの「生地」に3Dプリントする方式がハイブランドや大手メーカーにて採用されはじめています。
硬質素材だけではなく、ゴムのように柔軟性のある素材を含め、60万色フルカラーで3Dプリントできる機種があります(Stratasys J850 Prime FabriX)。
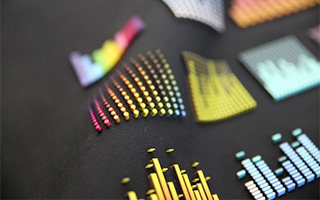
インクジェット方式の弱み
強度・耐久性についてはFDM方式に劣ります。
噴射した材料に光を照射し硬化させるため、太陽光での劣化もあります。その面では光造形方式と同じです。
どのようなシーンで選ぶべきか?
試作におけるデザイン性・外観の再現での用途では群を抜きます。
デザインの価値が高まる中、メーカーにおけるデザイン部門・設計部署での導入に最適です。
構想設計から最終段階まで、リアリティを持った試作品を気軽に何度も出し直しして調整しながら創ることが可能です。
Stratasysのインクジェット(PolyJet)方式について詳しい解説はこちら
バインダージェット方式
- 日本語表記:粉末接着方式
- ISO分類:結合材噴射法(Binder jetting)
- その他表記:バインダージェッティング方式
バインダージェット方式の概要
インクジェット方式(マテリアルジェッティング)は材料自体を噴射する方式でした。
それに対して、バインダージェット方式は、バインダー(=結合剤)の方を噴射することで造形物を固めます。
元々は石膏に結合剤を吹き付けて固める方式でした。
石膏という材質から後加工での着色がしやすく、フィギュアの造形や、簡易なデザインイメージの確認に用いられていました。
その後、金属、樹脂、セラミック等の材料でも造形できるようになり適用できる幅は広がりました。
尚、このバインダージェット方式の生みの親であるMITの研究者は、現在Desktop Metal社で金属3Dプリンターの開発に携わっています。
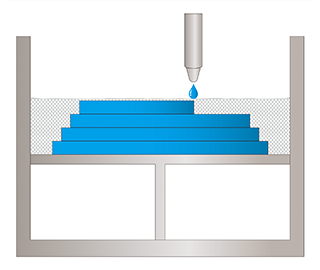
バインダージェット方式の強み
サポート材が不要であること、着色がしやすいこと、造形速度が速いことが挙げられます。
バインダージェット方式の弱点
表面精度が粗いこと、強度が弱いこと、粉末を取り扱い除去する必要があり、粉末の飛散による危険性や粉じん対策が必要であること、造形後に後処理の手間が掛かることが挙げられます。
どのようなシーンで選ぶべきか?
強度は求めないデザイン確認の用途に適合すると思います。
BMD方式
- 英語表記:Bound Metal Deposition方式
- ISO分類:-
- その他表記:ADAM方式(Atomic Diffusion Additive Manufacturing)
BMD方式の概要
金属3Dプリンターは金属粉を取り扱うため、取り扱いが容易ではありませんでした。
それを劇的に改善したのがBMD方式です。
BMD方式は、3つの段階を経て金属の造形物を作ります。
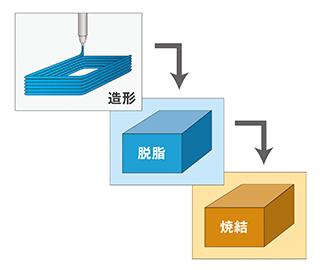
1.3Dプリンターでの造形
まず3Dプリンターで造形します。金属とポリマーとワックスでできた素材を熱で溶解し、積層します。
しかしこれだけでは金属部品として求められる物性が得られません。
そこで、次の段階に進みます。
2.専用の脱脂装置でバインダーを除去する
金属とバインダーが混ざった状態から、ワックスを除去します。
溶剤を用いた工程が不要となる新しい方式の装置が登場しています。
3.専用の焼結装置で焼結する
ピーク温度1400℃で焼結し、固めます。
これは製造業の世界では歴史があるMIM(Metal Injection Molding)の技術を応用したものです。
製品としてはこの金属3Dプリンターを含む3つの装置を1つのシステムとして提供する形式で販売されています。
BMD方式の強み
従来の金属3Dプリンターと異なり、専用の部屋を用意する必要がありません。
従来方式では、金属粉の粉塵対策、不活性化ガスを用いるための設備投資等、総合して投資規模・総保有コストが大きくなりがちでしたが、それを解決しています。
また、3Dプリンター本体はFDM方式で造形するため、従来工法では実現できなかった複雑な形状も精度高く造形可能です。
金属3Dプリンターの導入をためらっていた企業様にこそ検討いただきたい方式です。
BMD方式の弱点
焼結の際にガスを使います。このガスのランニングコストも導入判断の評価ポイントになるでしょう。
ただし、ガスの使用量は機種によって大きな差があります。
また、有機溶剤を扱うため、オフィスで使うには局所排気装置が必要になります。
(しかし、総保有コストを考えると圧倒的な削減ができると言って良いでしょう。)
どのようなシーンで選ぶべきか?
金属素材で低コストに造形したい、金属の製品開発を高速化したい、金属パーツの多品種少量生産に使いたいといったシーンでは最適な方式です。
BMD方式の3Dプリンター Desktop Metal特設ページはこちら
パウダーベッド方式
- ISO分類:粉末床溶融結合法(Powder Bed Fusion)
- その他表記:PBF方式
パウダーベッド方式の中には、レーザー熱源方式と、電子ビーム熱源方式があります。
- レーザビーム熱源方式(Selective Laser Melting/SLM)
- 電子ビーム熱源方式(Electron Beam melting/EBM)
パウダーベッド方式の概要
パウダーベッド方式は、金属粉末を敷き詰めた床に光線を照射し、その熱で焼結させる方式です。
金属のほかにナイロンや樹脂も用いられるケースがあります。
従来は金属を3Dプリンターで造形する際の主要な方式でした。
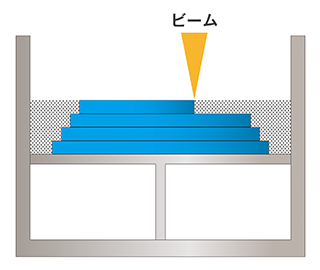
方式1.レーザー熱源方式
ハイパワーなレーザー光を照射することで金属粉末を焼結させます。
方式2.電子ビーム熱源方式
レーザーではなく電子ビームを照射する方式です。
レーザー熱源方式では難しかった銅の造形も可能な方式です。
パウダーベッド方式の強み
BMD方式の登場で情勢は変わっていますが、金属を造形できる3Dプリンターとして有力な方式であったと言えます。
パウダーベッド方式の弱点
機器本体が高額であるということに加え、工場において設置する部屋の確保、粉塵対策・不活性化ガスの排出対策の空調設備など、装置外の投資規模が大きくなること。 オペレーターが金属粉末を吸入するリスク、金属粉末が工場内に拡散するリスクがあること。
サポート材の除去に手間が掛かること、表面がざらついた造形物になること、などが挙げられます。
どのようなシーンで選ぶべきか?
現時点では、まずパウダーベッド方式の弱点を克服したBMD方式を検討いただき、BMD方式では適合しない場合にパウダーベッド方式をあわせて検討いただくというのが良いと思います。
シート積層法
- ISO分類:シート積層法(Sheet Lamination)
シート積層法の概要
シート積層法は、薄いシートを重ね合わせて、接着剤や超音波で結合させる方式です。
結合した素材をレーザーでカットし成形します。
シート積層法の強み
PVC、金属、紙等、他の方式ではあまり見られない材料を用いて造形可能です。
また、複数の金属素材を合わせて使うことができること等が挙げられます。
シート積層法の弱点
廃棄材料が多く出る可能性があること、他の方式に比べ造形精度が低いこと、中空構造が作りにくいこと、等が挙げられます。
どのようなシーンで選ぶべきか?
紙やPVCで造形したい場合、異なる金属素材を接合して用いたい場合などのシーンで有効になると思います。
指向性エネルギー堆積法
- ISO分類:指向性エネルギー堆積法(Directed Energy Deposition)
- その他表記:レーザーデポジション、レーザーメタルデポジション(LMD)
指向性エネルギー堆積法の概要
指向性エネルギー堆積法は、金属粉末を吹き付けながらレーザー光を照射することで肉盛り溶接する方式です。
指向性エネルギー堆積法の強み
金属の造形物ができること、異種材料を組み合わせて母材とは異なる金属の造形ができること、高熱で溶融するため耐久性が高い造形物ができること。また、大型造形が得意で造形速度も速い。
指向性エネルギー堆積法の弱点
金属粉末を扱うため取り扱いに注意を要すること、表面は粗い仕上がりになること、造形できる形状に制約が大きいこと等が挙げられます。
どのようなシーンで選ぶべきか?
こちらも、まず従来型金属3Dプリンターの弱点を克服したBMD方式を検討いただき、BMD方式では適合しない場合に指向性エネルギー堆積法の機種を検討いただくというのが良いと思います。
CIM(Cast in motion)方式
CIMではまず「型を造るための枠」を3Dプリンターで高速造形します。その枠の中にエポキシ樹脂を流し込み、それが型になります。このエポキシ樹脂は熱硬化性樹脂のため、オーブンで加熱し固めることで機械的特性に優れた型が得られます。
型を造形するために用いた枠は、水に浸すとフレーク状に砕けるため容易に除去可能です。造形した型は、表面精度を高めるため切削加工で研磨する等、仕上げ処理を施して完成です。
型を造形するCIM方式
FRP用の成形型などにおいては、型を3Dプリンターで造形する方式が実用化されています。
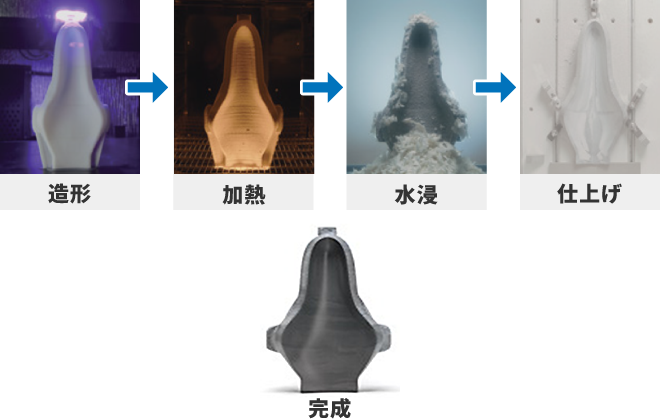
アルテックがお手伝いできること
3Dプリンターには様々な方式があり、非常に多くのメーカーがあります。
アルテックではお客様のニーズにお応えする上で、実績があり信頼性が高く、時代に適合したベストだと思えるメーカーのみ、厳選して取り扱っております。
3Dプリンター製品